Soldato
- Joined
- 6 Nov 2002
- Posts
- 9,960
- Location
- London UK
Asked in the purchased item thread (and on BYOAC) to post a build log so here's a quick and dirty one I knocked up today.
Taken me an absolute age (on and off for the past year) but this coffee table come arcade machine is now done. The CoffeeCade:-
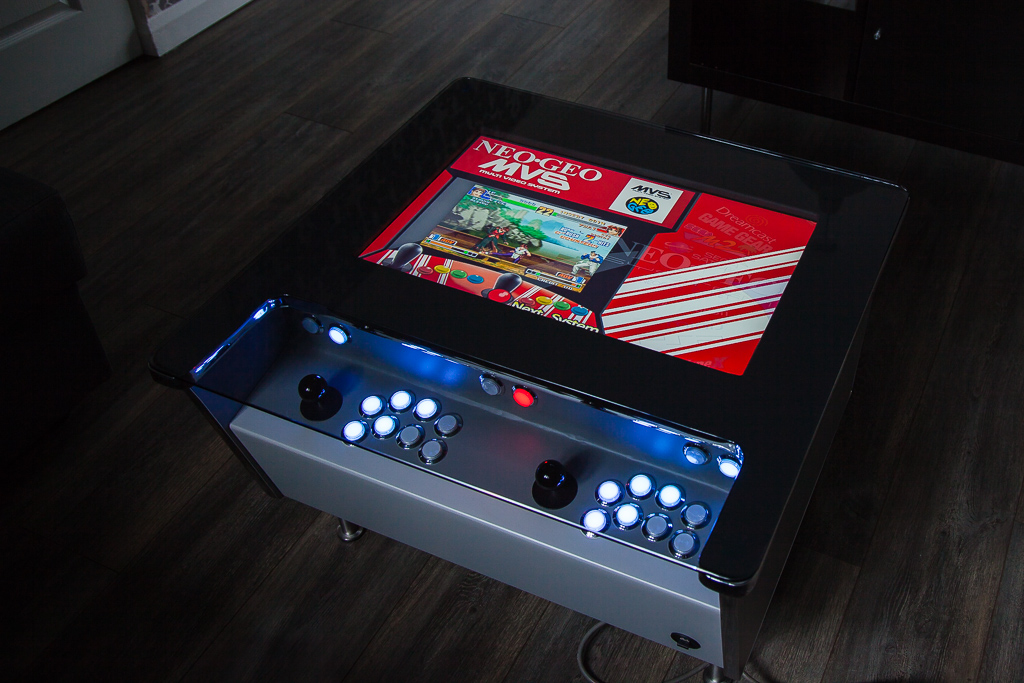
CoffeeCade 01 by Andy Baker, on Flickr
The Concept
I wanted an arcade machine that could be placed in the house without looking too much like an arcade machine which would be used as a game encyclopaedia for nostalgia purposes rather than full on gaming.
About 10 years ago I mocked up a cocktail cabinet for this but never got around to making it. Revisiting 10 years later and so much had changed so I decided to just re-design from scratch.
My criteria
Anyway this is what I came up with:-
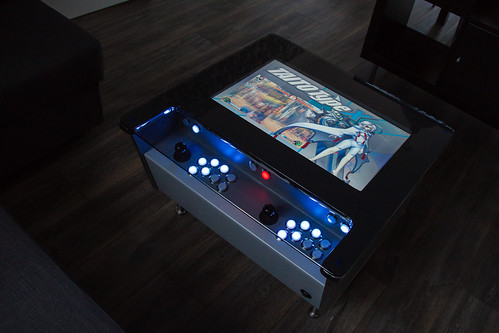
CoffeeCade 02 by Andy Baker, on Flickr

CoffeeCade 03 by Andy Baker, on Flickr
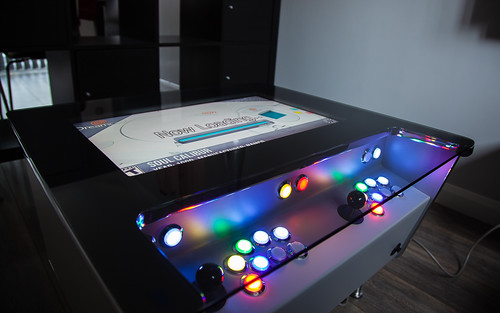
CoffeeCade 04 by Andy Baker, on Flickr
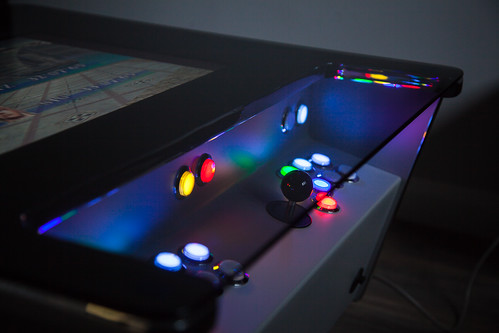
CoffeeCade 05 by Andy Baker, on Flickr
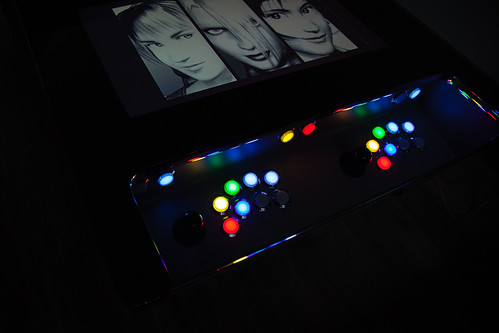
CoffeeCade 06 by Andy Baker, on Flickr
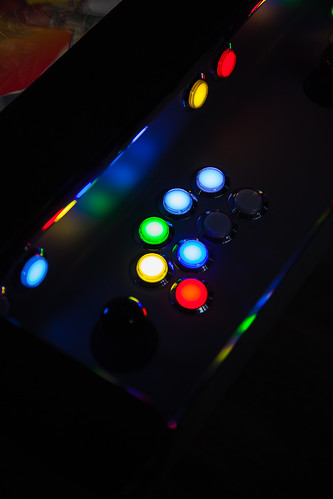
CoffeeCade 07 by Andy Baker, on Flickr
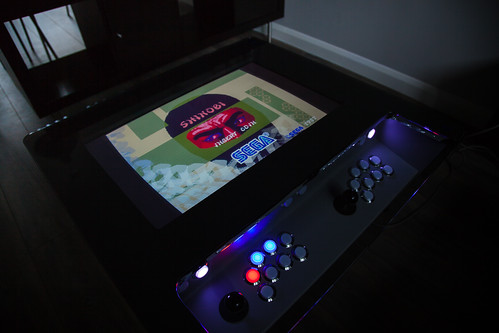
CoffeeCade 08 by Andy Baker, on Flickr
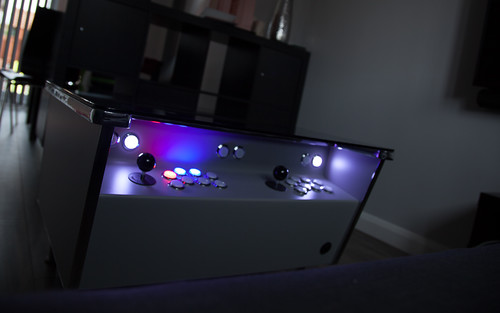
CoffeeCade 09 by Andy Baker, on Flickr
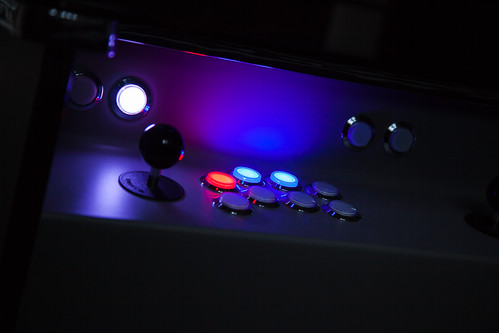
CoffeeCade 10 by Andy Baker, on Flickr
The Build
Firstly set about drafting a design in Sketch-up and after several revisions I came up with the following:-
In parallel I worked on the controls and software; So much has changed over the past ten years so lots of new options and toys to consider.
I opted for a MiniPac with the pre-assembled wiring harness, PacLED64 and UltraLux buttons for some flashy but cheesy lighting (illuminated buttons are all new to me).
With the aid of a empty ice cream container and tupperware box I now had a coupe of prototype controllers. First was to test stick/buttons before ordering more. Second was a full set of single player controls so I could work on config.
This then hooked up to a cheap PC i put together (MSI Z97, 8GB DDR3, Intel Pentium K Anniversary G3258, SSD for O/S, external USB3 drive for roms/data) running Win8.1 and HyperSpin as my fronted. Everything ran very well but later added a cheap Nvida GFX card for Mame HLSL and improvements to some of the heavier console emulation.
With design and internals in hand it was on to cabinet fabrication but first a quick cardboard mock-up to give me a feel for size and layout.
Everything was to be made from 18mm MDF using a plunge rail saw for straight cuts and a mixture of jigsaw and router for curves and bevels. Side pieces and top also had a t-molding slot cut using router and appropriate bit.
Having everything measured up in Sketchup first meant cutting the panels took no time at all.
I used fixing blocks similar to these which allow me to assembly/disassemble throughout the fabrication without having to re-screw any of the MDF (which never ends well).
Side and rear panels were straight forward but I also wanted the front section to be seamless so this is made from three separate pieces, some filler, and LOTS of sanding.
I also wanted to hide as much of the gubbins as possible so speakers, fans, amp controls, switches were all to be mounted on the base. Leaving just games controls and a double USB port on show.
Used the fans and speakers to mark out positions then cut the holes with a jigsaw and bevelled the edges with the router. The results were far from perfect but as this was on the bottom I wasn’t too fussed.
The speakers themselves were an ancient pair of MB Quarts I had in one of my cars probably 20 years ago. However old they were pretty damm good (i.e. expensive) from what I recalled so thought I’d try them out. Probably overkill for purpose but keeps the cost down. Both powered by a little Lepai LP-A6FM amp.
Legs which match another another piece of furniture in the room are from Ikea called Captia. Here I made a mistake, I positioned the speaker/fan holes too close to the corners of the base meaning part of the leg fixing brackets over hang. This was easy to rectify by taking the Dremel to them and notching off a corner on each.
The top panel I don’t have appeared to have taken any pics of whilst cutting, but the only real interesting (‘ish) bit here was I routed approx 8mm off the bottom of it where the un-cased monitor would fit. Not only did this bring the screen closer to the glass top but also created a snug fit to put the screen into, therefore no issues with placement/alignment when taking the screen in and out. I also bevelled the top side around the screen edge.
With most of the basic fabrication done it was re-assembly to see if everything fit.
Quick trial placement of components then time to take it all apart again.
I originally wanted to cover the cabinet with laminate but due to the curved front piece it wasn’t going to be practical. I did look into heating and bending options but seems you need some specialised equipment. So after looking about at options (wanting to avoid painting) I found a sticky back vinyl wrap material. The finish is great as long as the surface welll prepared. And by well prepared I mean it will show the most minor of defects so lots and lots of filling, priming and sanding to be done.
Covered the base panel and fitted the legs
I opted for a flat medium grey which went well with the room it was going in. Supplier incorrectly sent me a lighter grey first but let me keep it so I decided to use that on the inside to keep things tidy. Speakers, fans, and switches fitted.
The notch out on the left is for the amp controls.
The front panel was without doubt the hardness piece to prep for vinyl, it actually took me two attempts requiring some extra vinyl to be ordered. First time round I found that joins between the pieces were visible plus I managed to stretch a bit of the vinyl whilst going round the buttons holes which meant it wouldn’t lay flat afterwards.
Doh!!
I used P38 for filling (the stuff you use on car bodywork) but it’s also fantastic for wood work, very easy to work with and sand, with the added bonus it does not shrink.
Second attempt and now happy with the finish.
Vinyl covering holes trimmed and buttons fitted.
As this point I finally felt things were coming together and it was on to final assembly. Controls fitted and wired up.
Recently built some PAX wardrobes from Ikea and the glass fronts come in packaging which contained strips of rubber/foam (~15mm square). This stuff is brilliant for mounting all the components on, keeps everything off base and also acts as a vibration dampener to reduce noise. Can see some of it in the bottom left of this photo.
Then one by one, adding all the bits and screwed them down. The fixing blocks worked great and I’ve also laid things out so sections can be (if needed) dissembled without have to cut/break anything.
Hooked it up to the TV to test wiring before putting the top panel which makes access a little harder.
I originally went for a black finish on the top piece but once fitted (only first coat applied) I wasn’t happy with it, far too dark.
So off it came, sanded down and then applied a grey paint that was intentionally a little darker than the cabinet vinyl; happy with this the t-molding was applied.
Screen fitted (made simple brackets out of MDF) and attached to cabinet.
I think the only other thing I haven’t got a photo of is the power setup. The C14 inlet feeds power to a single power socket like the below which is mounted to the inside side panel. Plugged into this is a smart socket so when the PC is powered on it then also feeds power to the screen and audio amp.
Glass came from a local firm, it took a lot longer than expected due to a couple of mishaps but happy with the results. It’s 6mm toughened, bronze tinted (which looks grey), with edges rounded and polished. They even put the kite mark and info required by regs along the edge to keep the top clean.
Overall I’ve really pleased with how this project turned out, would I make any changes? Yes but I think just one, and that would be thicker vinyl to reduce the amount of prep work, but hey I can do that with the next project.
Taken me an absolute age (on and off for the past year) but this coffee table come arcade machine is now done. The CoffeeCade:-
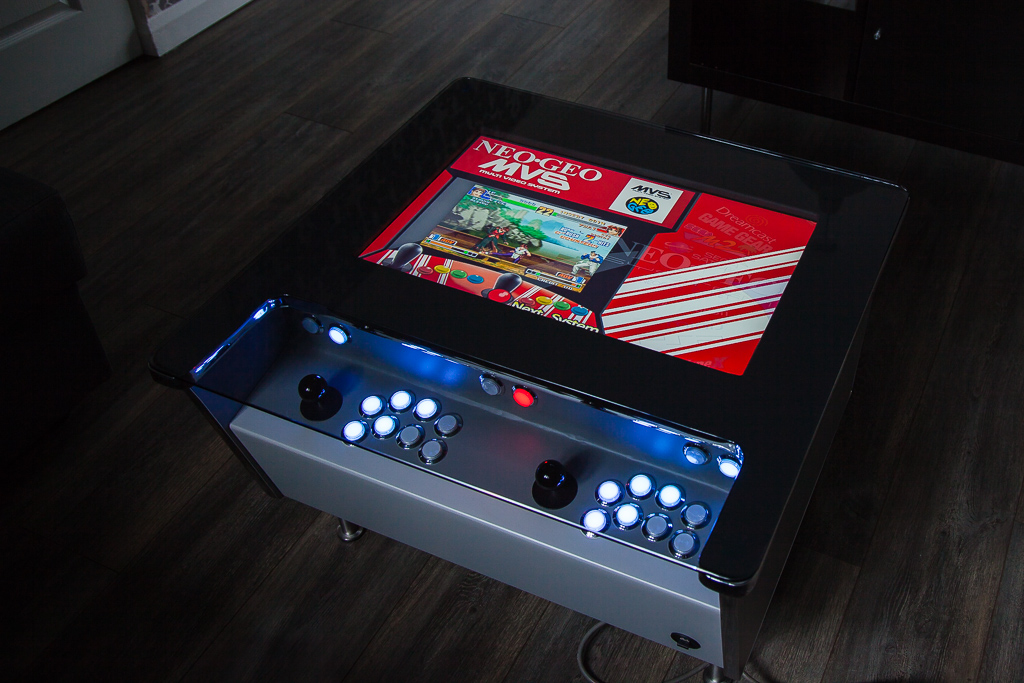
CoffeeCade 01 by Andy Baker, on Flickr
The Concept
I wanted an arcade machine that could be placed in the house without looking too much like an arcade machine which would be used as a game encyclopaedia for nostalgia purposes rather than full on gaming.
About 10 years ago I mocked up a cocktail cabinet for this but never got around to making it. Revisiting 10 years later and so much had changed so I decided to just re-design from scratch.
My criteria
- Ability to play both Arcade and retro Console games
- 2 Player, want it to be a social thing
- Focused more towards horizontal games
- To be used as a coffee table so glass top and limited height
- Side by side controls so it can be played from sofa
- Small foot print but big enough to be used comfortably
- Controls not prominent
Anyway this is what I came up with:-
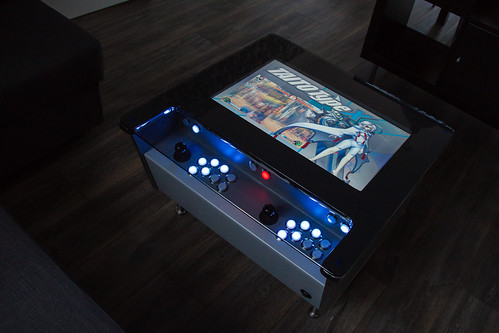
CoffeeCade 02 by Andy Baker, on Flickr

CoffeeCade 03 by Andy Baker, on Flickr
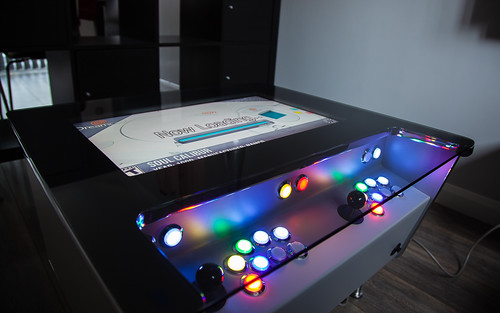
CoffeeCade 04 by Andy Baker, on Flickr
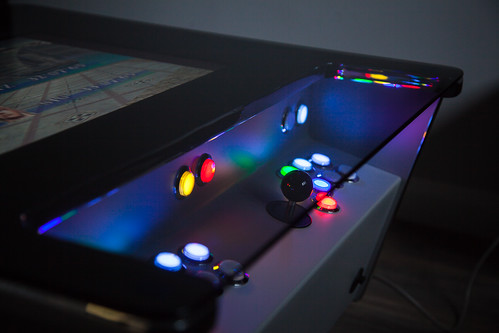
CoffeeCade 05 by Andy Baker, on Flickr
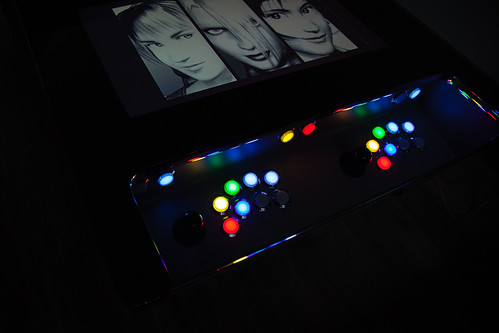
CoffeeCade 06 by Andy Baker, on Flickr
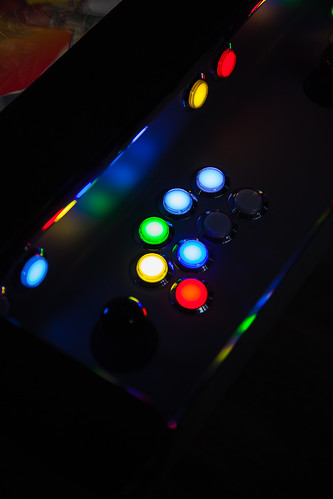
CoffeeCade 07 by Andy Baker, on Flickr
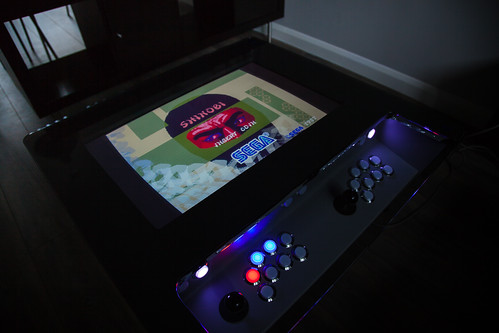
CoffeeCade 08 by Andy Baker, on Flickr
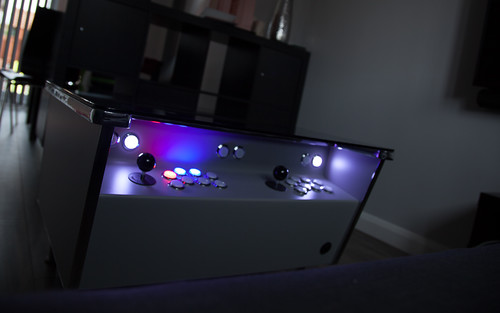
CoffeeCade 09 by Andy Baker, on Flickr
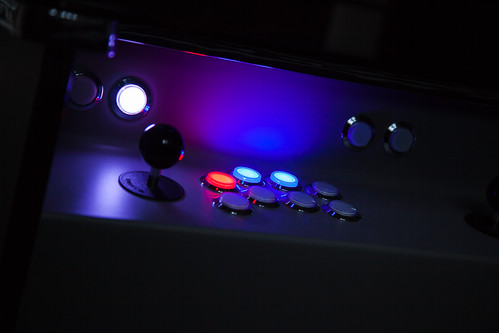
CoffeeCade 10 by Andy Baker, on Flickr
The Build
Firstly set about drafting a design in Sketch-up and after several revisions I came up with the following:-


In parallel I worked on the controls and software; So much has changed over the past ten years so lots of new options and toys to consider.
I opted for a MiniPac with the pre-assembled wiring harness, PacLED64 and UltraLux buttons for some flashy but cheesy lighting (illuminated buttons are all new to me).
With the aid of a empty ice cream container and tupperware box I now had a coupe of prototype controllers. First was to test stick/buttons before ordering more. Second was a full set of single player controls so I could work on config.


This then hooked up to a cheap PC i put together (MSI Z97, 8GB DDR3, Intel Pentium K Anniversary G3258, SSD for O/S, external USB3 drive for roms/data) running Win8.1 and HyperSpin as my fronted. Everything ran very well but later added a cheap Nvida GFX card for Mame HLSL and improvements to some of the heavier console emulation.
With design and internals in hand it was on to cabinet fabrication but first a quick cardboard mock-up to give me a feel for size and layout.



Everything was to be made from 18mm MDF using a plunge rail saw for straight cuts and a mixture of jigsaw and router for curves and bevels. Side pieces and top also had a t-molding slot cut using router and appropriate bit.
Having everything measured up in Sketchup first meant cutting the panels took no time at all.



I used fixing blocks similar to these which allow me to assembly/disassemble throughout the fabrication without having to re-screw any of the MDF (which never ends well).


Side and rear panels were straight forward but I also wanted the front section to be seamless so this is made from three separate pieces, some filler, and LOTS of sanding.


I also wanted to hide as much of the gubbins as possible so speakers, fans, amp controls, switches were all to be mounted on the base. Leaving just games controls and a double USB port on show.
Used the fans and speakers to mark out positions then cut the holes with a jigsaw and bevelled the edges with the router. The results were far from perfect but as this was on the bottom I wasn’t too fussed.


The speakers themselves were an ancient pair of MB Quarts I had in one of my cars probably 20 years ago. However old they were pretty damm good (i.e. expensive) from what I recalled so thought I’d try them out. Probably overkill for purpose but keeps the cost down. Both powered by a little Lepai LP-A6FM amp.
Legs which match another another piece of furniture in the room are from Ikea called Captia. Here I made a mistake, I positioned the speaker/fan holes too close to the corners of the base meaning part of the leg fixing brackets over hang. This was easy to rectify by taking the Dremel to them and notching off a corner on each.
The top panel I don’t have appeared to have taken any pics of whilst cutting, but the only real interesting (‘ish) bit here was I routed approx 8mm off the bottom of it where the un-cased monitor would fit. Not only did this bring the screen closer to the glass top but also created a snug fit to put the screen into, therefore no issues with placement/alignment when taking the screen in and out. I also bevelled the top side around the screen edge.
With most of the basic fabrication done it was re-assembly to see if everything fit.




Quick trial placement of components then time to take it all apart again.


I originally wanted to cover the cabinet with laminate but due to the curved front piece it wasn’t going to be practical. I did look into heating and bending options but seems you need some specialised equipment. So after looking about at options (wanting to avoid painting) I found a sticky back vinyl wrap material. The finish is great as long as the surface welll prepared. And by well prepared I mean it will show the most minor of defects so lots and lots of filling, priming and sanding to be done.
Covered the base panel and fitted the legs

I opted for a flat medium grey which went well with the room it was going in. Supplier incorrectly sent me a lighter grey first but let me keep it so I decided to use that on the inside to keep things tidy. Speakers, fans, and switches fitted.


The notch out on the left is for the amp controls.
The front panel was without doubt the hardness piece to prep for vinyl, it actually took me two attempts requiring some extra vinyl to be ordered. First time round I found that joins between the pieces were visible plus I managed to stretch a bit of the vinyl whilst going round the buttons holes which meant it wouldn’t lay flat afterwards.


Doh!!

I used P38 for filling (the stuff you use on car bodywork) but it’s also fantastic for wood work, very easy to work with and sand, with the added bonus it does not shrink.
Second attempt and now happy with the finish.

Vinyl covering holes trimmed and buttons fitted.


As this point I finally felt things were coming together and it was on to final assembly. Controls fitted and wired up.

Recently built some PAX wardrobes from Ikea and the glass fronts come in packaging which contained strips of rubber/foam (~15mm square). This stuff is brilliant for mounting all the components on, keeps everything off base and also acts as a vibration dampener to reduce noise. Can see some of it in the bottom left of this photo.

Then one by one, adding all the bits and screwed them down. The fixing blocks worked great and I’ve also laid things out so sections can be (if needed) dissembled without have to cut/break anything.



Hooked it up to the TV to test wiring before putting the top panel which makes access a little harder.


I originally went for a black finish on the top piece but once fitted (only first coat applied) I wasn’t happy with it, far too dark.

So off it came, sanded down and then applied a grey paint that was intentionally a little darker than the cabinet vinyl; happy with this the t-molding was applied.

Screen fitted (made simple brackets out of MDF) and attached to cabinet.

I think the only other thing I haven’t got a photo of is the power setup. The C14 inlet feeds power to a single power socket like the below which is mounted to the inside side panel. Plugged into this is a smart socket so when the PC is powered on it then also feeds power to the screen and audio amp.


Glass came from a local firm, it took a lot longer than expected due to a couple of mishaps but happy with the results. It’s 6mm toughened, bronze tinted (which looks grey), with edges rounded and polished. They even put the kite mark and info required by regs along the edge to keep the top clean.
Overall I’ve really pleased with how this project turned out, would I make any changes? Yes but I think just one, and that would be thicker vinyl to reduce the amount of prep work, but hey I can do that with the next project.