Associate
Hi, What is the way to connect/attach this watercooling plate 25*30mm to this BLHeli ESC 70a 21*42mm to get the most cooling efficiency?
- Water-cooling plate (30.5x25mm): https://www.aliexpress.com/item/1005001807716093.html?skuId=12000017701193167
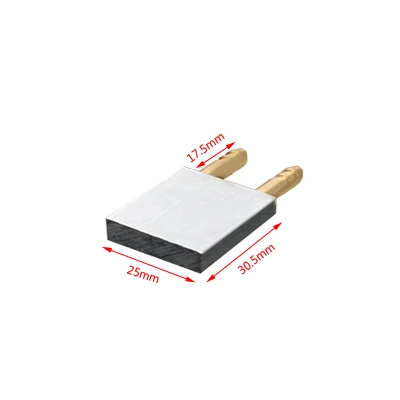
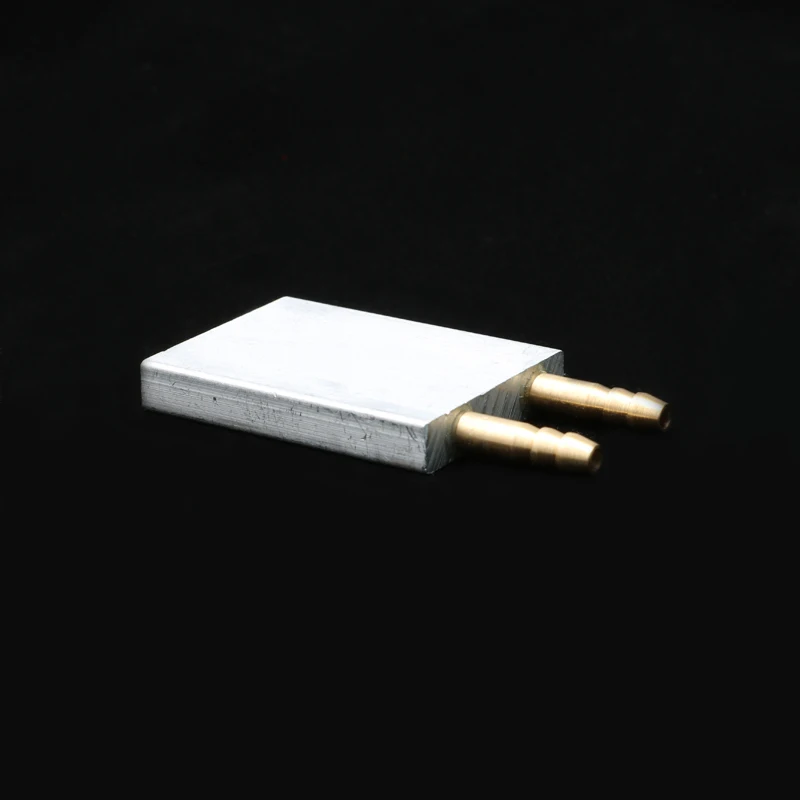
- BLHeli ESC 70a board 21*42mm: https://www.aliexpress.com/item/1005002438042950.html
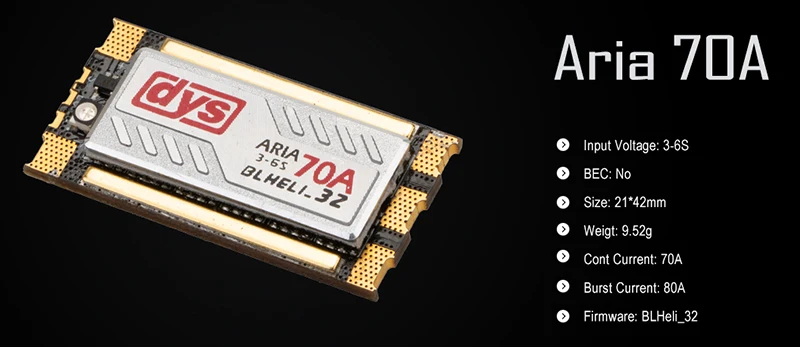
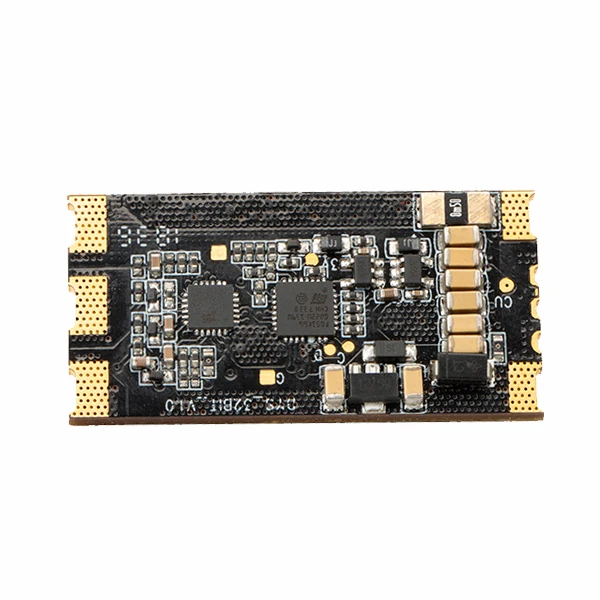