Cutting, bending and fitting the rigid tubing. The tubing is 12mm ID / 16mm OD, which meant the bend radius was quite large.
This post shows a test fill with clear coolant - this will soon be replaced with a custom Purple pastel coolant from Mayhems...
Tools for cutting and bending
First tubes in place - reservoir inlet and outlet, and fill port routing to the rear of the case
90º bending mandrel. As it turned out, a tighter bend radius was needed...
Improvised tight bend 90º jig, using the original mandrels for alignment, and a plastic bottle cut and nailed down for the bend itself
Bending a tube with the new tight 90º jig
Another improvised jig, used to secure the bent tube while bending again in a perpendicular plane. This gave perfectly-aligned bends
An improvised tight radius 45º jig, again using the mandrels as guides for the tubing
All bends done, tubing prepped and finished, and fitted in the system
Test filling the loop with clear coolant. This was followed by a (successful) extended leak test. The coolant will soon be replaced with a custom purple pastel coolant from Mayhems
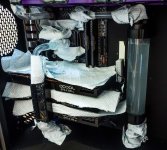