Ok some people will think I'm crazy allot of my friends did, i had planned on buying a SG03 i love them they gorgeous and tiny to boot i was all set, then one morning i woke up and decided hey what the hell ill make my own.
All i have heard ever since is why! it certainly isn't cheaper considering i have had to bye all the tools materials etc, but its mine and i made it
So here we go I'm going for a desktop htpc style case made from aluminum (and stainless mesh as the ally mesh was to hard to source)
This is what it will be sitting next to or on top of
Got the delivery with a few goodies but I'm still waiting on some parts but this is enough for me to make a start at least
This is the aluminum, i got a good deal on this from a gangway manufacturer all precut to size extremely accurate with a guillotine.
All i have heard ever since is why! it certainly isn't cheaper considering i have had to bye all the tools materials etc, but its mine and i made it

So here we go I'm going for a desktop htpc style case made from aluminum (and stainless mesh as the ally mesh was to hard to source)
This is what it will be sitting next to or on top of

Got the delivery with a few goodies but I'm still waiting on some parts but this is enough for me to make a start at least

This is the aluminum, i got a good deal on this from a gangway manufacturer all precut to size extremely accurate with a guillotine.
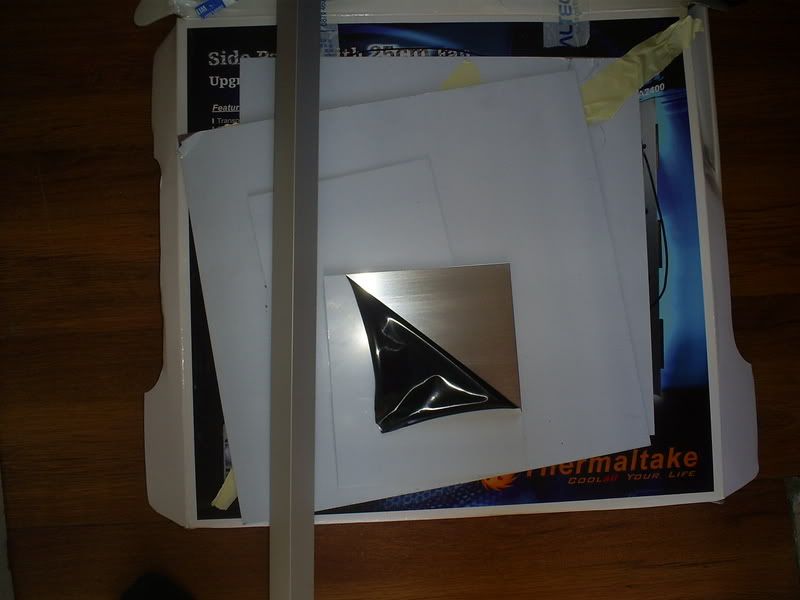
Last edited: