Hi all, I know a lot of you are interested in build projects so I thought I'd start a thread on something I've been wanting to make for a long time.
It's nice to document the progress and have an on-line diary of how things are going. Any support will drive me onto the finish too.
I use hand planes every day and I've always lusted after a high quality bespoke plane, like a Lazarus, Holtey, Bill Carter etc but the price of these planes can go into the thousands and my pockets just aren't deep enough.
So making one is the next best thing. The only trouble is I've never done a day of metal work in my life.
Woodwork yes but metal work is a whole other ball game.
So how well this project will turn out is any ones guess.
I've done a fair few hours research into making infill planes and am confident in the process...mostly.
I've taken a lot of inspiration from Carter's and Lazurus planes, both makers are at the pinnacle of their career and the planes they produce are amazing.
So i think the best thing to do is get stuck in!
First things first I ordered some 4mm CZ108 brass 300mm long by 100mm wide.
I then cut it in half on the band saw.
I made a paper template of the sides of the plane working out the dovetail spacing.
And again cut them roughly on the band saw.
That little lot was enough for one evening.
As I'll only be working on the plane in the evenings its going to be a lengthy project but I'll keep this thread updated as and when more is done.
It's nice to document the progress and have an on-line diary of how things are going. Any support will drive me onto the finish too.
I use hand planes every day and I've always lusted after a high quality bespoke plane, like a Lazarus, Holtey, Bill Carter etc but the price of these planes can go into the thousands and my pockets just aren't deep enough.
So making one is the next best thing. The only trouble is I've never done a day of metal work in my life.
Woodwork yes but metal work is a whole other ball game.
So how well this project will turn out is any ones guess.
I've done a fair few hours research into making infill planes and am confident in the process...mostly.
I've taken a lot of inspiration from Carter's and Lazurus planes, both makers are at the pinnacle of their career and the planes they produce are amazing.
So i think the best thing to do is get stuck in!
First things first I ordered some 4mm CZ108 brass 300mm long by 100mm wide.
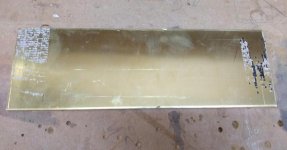
I then cut it in half on the band saw.
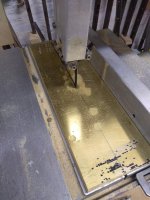
I made a paper template of the sides of the plane working out the dovetail spacing.

And again cut them roughly on the band saw.
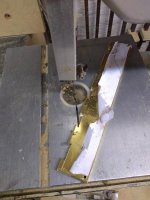
That little lot was enough for one evening.
As I'll only be working on the plane in the evenings its going to be a lengthy project but I'll keep this thread updated as and when more is done.
Last edited: