For the front knob I'm keeping with the theme of wood and metal.
I planed an straight edge on a piece of cherry wood, our over hand planer decided to break this morning so I pulled out an old jointer plane I made.
Next I went over to the engineering lathe. It doesn't get used much any more and tooling is sparse.
While I've done a fair amount of turning on our wood lathe I've only used this engineering lathe a hand full of times over the years and am only self taught (which equates to me probably doing every thing wrong)
I'm turning soft aluminium so it's not to bad. Here I'm machining the bottom part of the front knob.
From there I cut a piece of the cherry wood and fitted a threaded insert into the centre.
I then used epoxy to glue the aluminium to the cherry wood, using the bolt to pull them tight together.
Once the epoxy had cured I Glued the cherry to a sacrificial piece of wood that I could secure in the wood lathe.
Back to the familiarity of the wood lathe I turned the front knob to size.
Next I marked out and fitted another threaded insert into the maple infill.
And finally it's starting to resemble a plane.
With all of my fumbling with the engineering lathe that was time for another evening.
I planed an straight edge on a piece of cherry wood, our over hand planer decided to break this morning so I pulled out an old jointer plane I made.
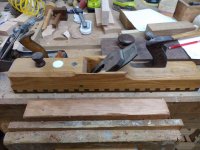
Next I went over to the engineering lathe. It doesn't get used much any more and tooling is sparse.
While I've done a fair amount of turning on our wood lathe I've only used this engineering lathe a hand full of times over the years and am only self taught (which equates to me probably doing every thing wrong)
I'm turning soft aluminium so it's not to bad. Here I'm machining the bottom part of the front knob.
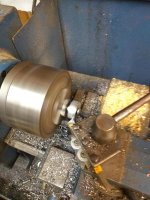
From there I cut a piece of the cherry wood and fitted a threaded insert into the centre.
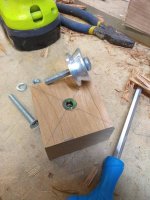
I then used epoxy to glue the aluminium to the cherry wood, using the bolt to pull them tight together.
Once the epoxy had cured I Glued the cherry to a sacrificial piece of wood that I could secure in the wood lathe.
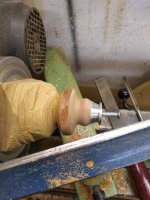
Back to the familiarity of the wood lathe I turned the front knob to size.
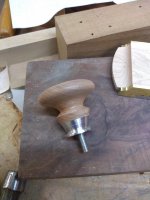
Next I marked out and fitted another threaded insert into the maple infill.
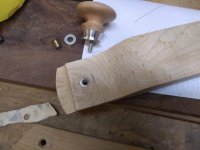
And finally it's starting to resemble a plane.
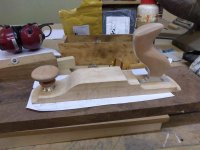
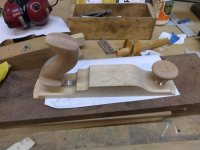
With all of my fumbling with the engineering lathe that was time for another evening.