Hi everyone !
A little while ago (2 months), I built my 1st ever hardline custom waterloop.
1 week ago, I had to move my PC from one room to the other one and the same day after 2hrs of gaming it started leaking. After investigation, it occurred that the end of the tube section was not perfectly round which I assume was the cause.
I bent the tube again with a precision which I'm quite proud of and tonight, 5 days later and again after 2hrs of gaming, it started leaking again, plus in the same spot.
The only obvious reason that comes to me is the pressure, as the tubes were very hot but is that a thing in water-cooling loops ? How should I handle it ?
FYI, when reinitialising the loop, I let it run 2hrs with fill port open then closed it.
Honestly I have strong doubt that my tubes could be wrong again which is why I'm coming to you : what reasons could cause my loop to leak for no obvious reason ?
I'll be glad to provide any helpful info, I'm feeling a bit desperate.
Thanks a lot
Vincent
A little while ago (2 months), I built my 1st ever hardline custom waterloop.
1 week ago, I had to move my PC from one room to the other one and the same day after 2hrs of gaming it started leaking. After investigation, it occurred that the end of the tube section was not perfectly round which I assume was the cause.
I bent the tube again with a precision which I'm quite proud of and tonight, 5 days later and again after 2hrs of gaming, it started leaking again, plus in the same spot.
The only obvious reason that comes to me is the pressure, as the tubes were very hot but is that a thing in water-cooling loops ? How should I handle it ?
FYI, when reinitialising the loop, I let it run 2hrs with fill port open then closed it.
Honestly I have strong doubt that my tubes could be wrong again which is why I'm coming to you : what reasons could cause my loop to leak for no obvious reason ?
I'll be glad to provide any helpful info, I'm feeling a bit desperate.
Thanks a lot
Vincent
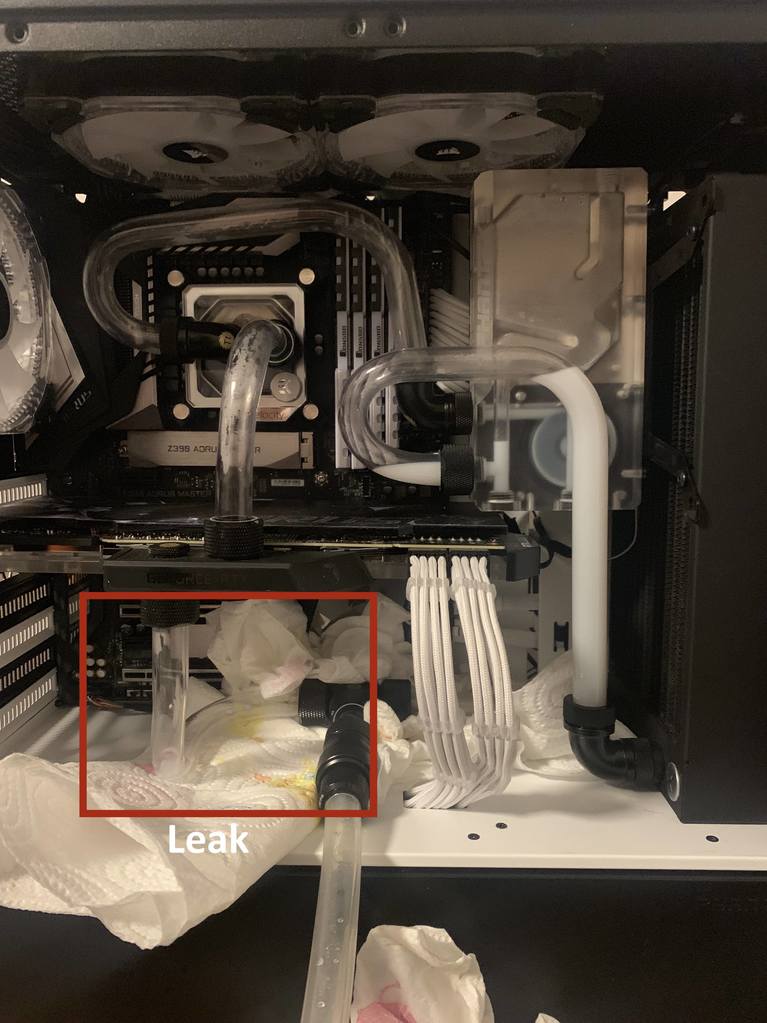