- Joined
- 13 Mar 2006
- Posts
- 6,712
Bit of progress - lots of small diamond filing of the resin manifolds (bit boring, no pics), and some sanding and polishing of the g1/4 bsp copper ports.
The case is upside down here - this is the drain port with an incompletely polished 1/4" right angle barbed connector with the 1m of 1/4" ID norprene drain pipe with a largely unsanded little 1/4" ball valve on the end. The norprene will be trimmed to around 35cm or so and the ball valve tucked away when finished.
Videos:
YouCut_20220618_221335882
YouCut_20220618_182149571
Photos:
20220618_181238_HDR
20220618_181044_HDR
The case is upside down here - this is the drain port with an incompletely polished 1/4" right angle barbed connector with the 1m of 1/4" ID norprene drain pipe with a largely unsanded little 1/4" ball valve on the end. The norprene will be trimmed to around 35cm or so and the ball valve tucked away when finished.
Videos:
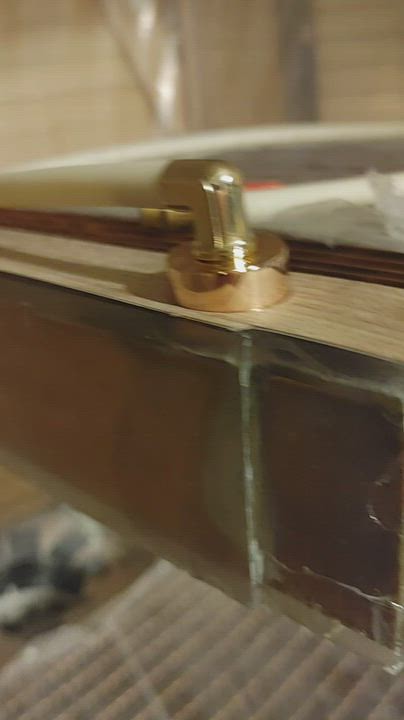

Photos:
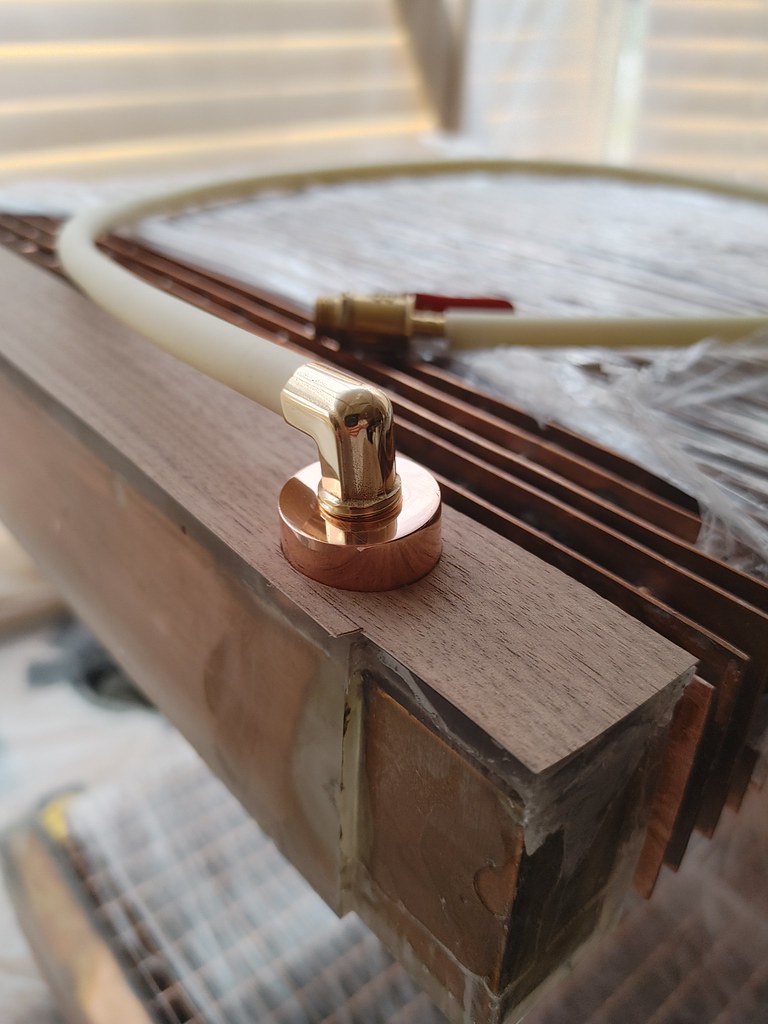

Last edited: