I know some of you people like project threads so thought i'd make one, however this one is gonna take ages as i don't have lots of spare time to work on this thing and i'm definately an amatuer at this kind of thing.
Back in October 2009 had a minor bump in my Capri 2.8i which due to me moving in with my girlfriend a few months later left me with no spare cash to pay for someone else to repair it (didn't want to use insurance) and at the time had no garage to work on it in, so it got left sat outside on the drive, in the rain, collecting bird poo and occasionally getting buried under large amounts of snow for about 20 Months.
Up until the and of July it was still sat there looking like this -
The actual accident resulted in a ruined front panel, headlight bowl (possibly salvageable), Bonnet (apparently repairable), wrecked bumper, and a slightly bent lower inner wing tip (again repairable) as well as misc bits like I need a new headlight & plastic bonnet lip.
I paid a fair bit to have the car resprayed about 6 years ago, as well as replace both rear arhces & rear lower 1/4 panels, it seems the company that did it did a pants job so their work is being re-done, i'm not even convinced they fully replaced the parts I paid for, guess i'll be finding out soon, it'll be interesting to see if any horrors lie underneath their work.
Now that the garage that me and my dad were building at his house is at a point that it is weathertight work can begin on it.
Thankfully i now have a decent amount of dry workspace
I also thought that by the time the car is done it'll have been off the road for 3-4 years so i'd buy it a little gift, it's also a nice incentive for me to keep at it on a weekend, picked this up on Monday along with all the electrics and ECU -
I'll stick some more pic's up later this evening of what's been done so far.
Back in October 2009 had a minor bump in my Capri 2.8i which due to me moving in with my girlfriend a few months later left me with no spare cash to pay for someone else to repair it (didn't want to use insurance) and at the time had no garage to work on it in, so it got left sat outside on the drive, in the rain, collecting bird poo and occasionally getting buried under large amounts of snow for about 20 Months.
Up until the and of July it was still sat there looking like this -
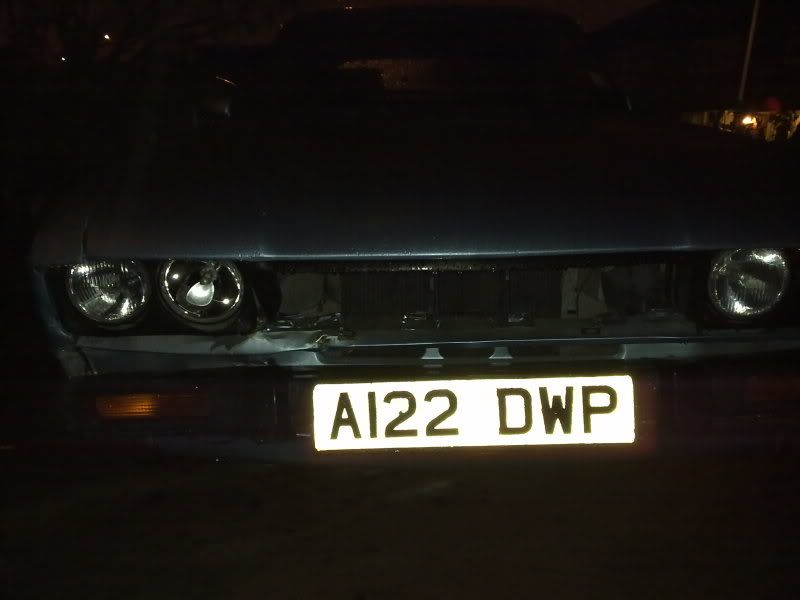
The actual accident resulted in a ruined front panel, headlight bowl (possibly salvageable), Bonnet (apparently repairable), wrecked bumper, and a slightly bent lower inner wing tip (again repairable) as well as misc bits like I need a new headlight & plastic bonnet lip.
I paid a fair bit to have the car resprayed about 6 years ago, as well as replace both rear arhces & rear lower 1/4 panels, it seems the company that did it did a pants job so their work is being re-done, i'm not even convinced they fully replaced the parts I paid for, guess i'll be finding out soon, it'll be interesting to see if any horrors lie underneath their work.
Now that the garage that me and my dad were building at his house is at a point that it is weathertight work can begin on it.
Thankfully i now have a decent amount of dry workspace

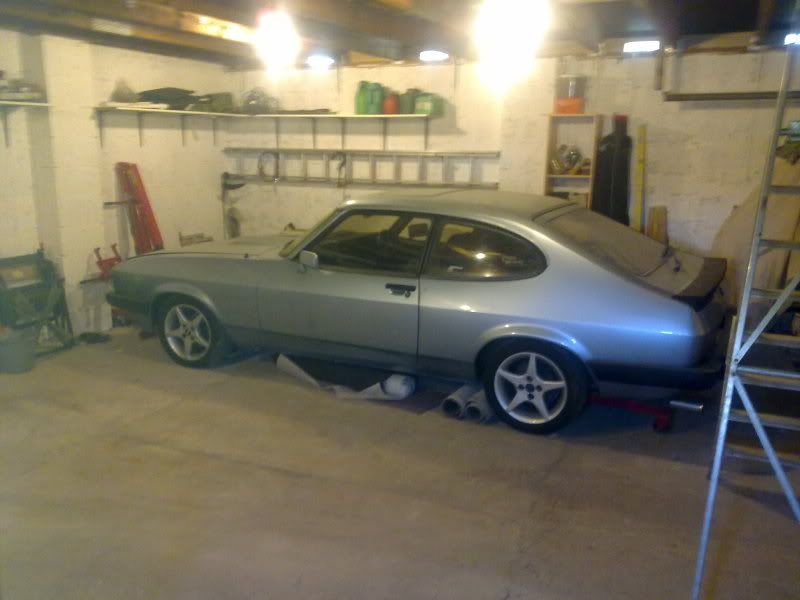
I also thought that by the time the car is done it'll have been off the road for 3-4 years so i'd buy it a little gift, it's also a nice incentive for me to keep at it on a weekend, picked this up on Monday along with all the electrics and ECU -

I'll stick some more pic's up later this evening of what's been done so far.