All that building and rebuilding has paid off, looking slick mate! Only shame is those pumps being hidden away on the PSU side, might have to go all redneck again and build Lian Li D80000![]()
I am tempted to do that as there's a reasonable amount of space at the front, might be for a future mod though... Unless I get creative this evening while I do some copper work

Last night had about 30 mins and got this fiddly small section in, joins the top two rads from back to front:

Using this offcut with some white tape to mark on the pipes the fully inserted depth to make sure the fit is as perfect as it can be (its not as simple as PETG...).
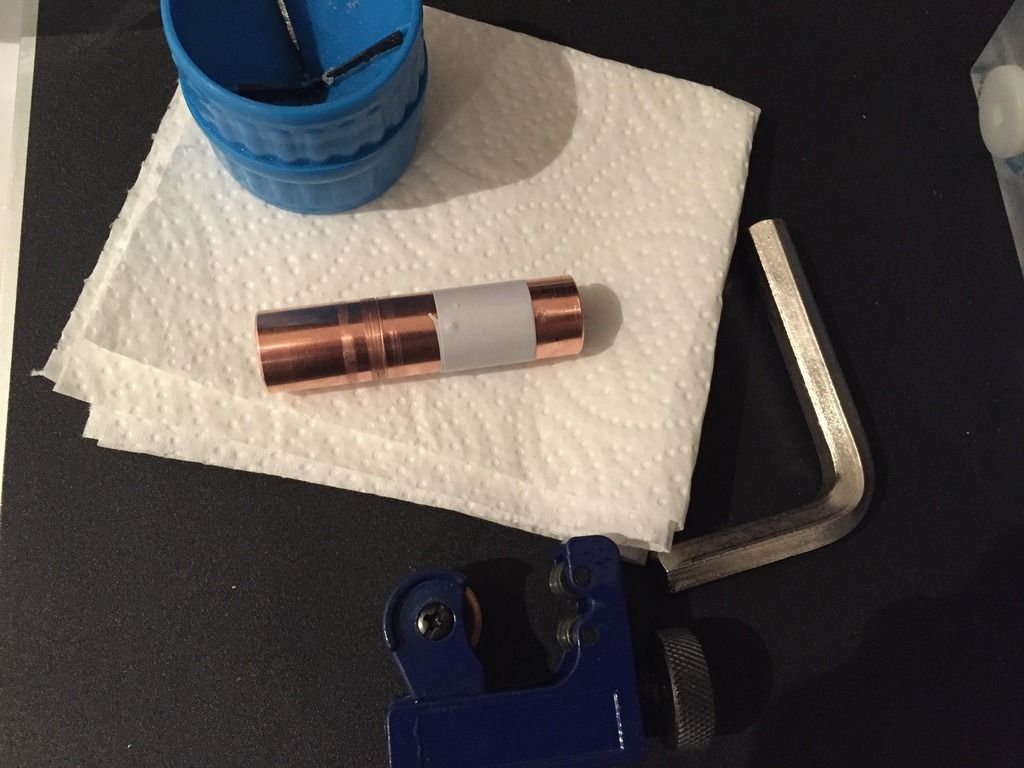
The nice museum wax turned up so I can now finish off the pipes after polishing, wish me luck bending later
