@deuse And anybody else who is taking an interest. I am so close to finishing this rebuild now! ive got the new extruder on and set all I need to do is run a few new wires and finish some firmware changes. The list of new bits it can do are pretty awesome.
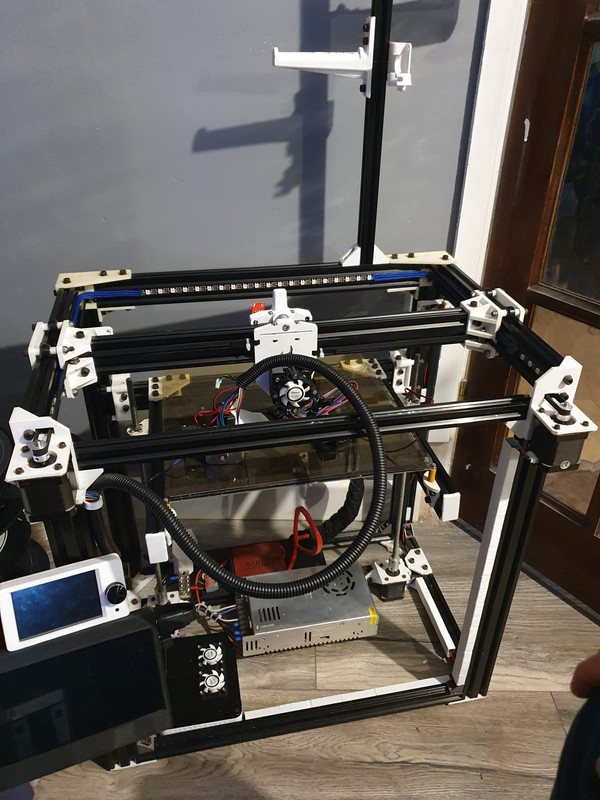
This most recent bunch of upgrades adds the following.
1) The pi3 can turn the printer on and off via octoprint and the psu control addin. Wired up via a 3.3v relay.
2) 28 individually adressable leds individually controlable via octoprint and the Ws281x LED status plugin. (More on this later)
3) Titan aero clone, new bed springs, new belts, new pully bearings, new t8's, new antibacklash nuts.
4) pi cam. Not yet installed.
I think im about to pull out the last few original wires. Also @deuse this bed glass sheet flexi thing... where did you buy it.. I think I need a new one as i've managed to dig into it with something and there is a little gouge out of it
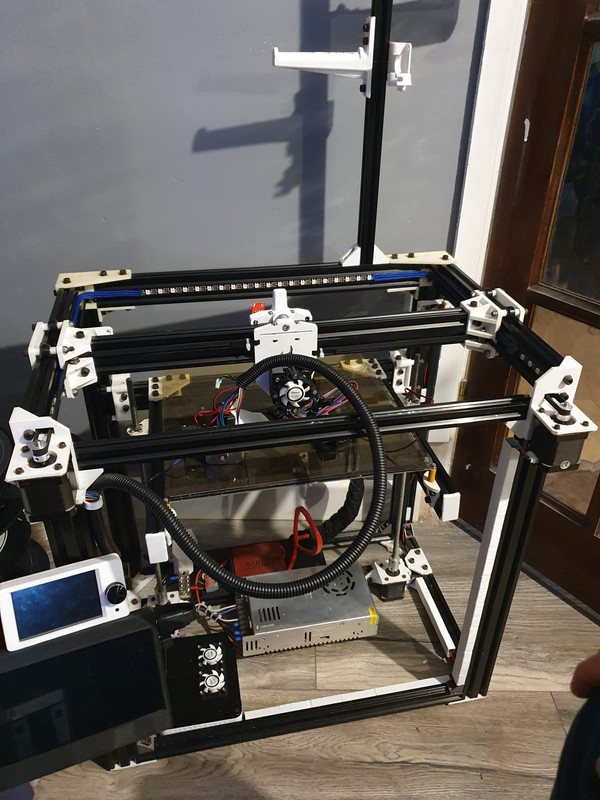
This most recent bunch of upgrades adds the following.
1) The pi3 can turn the printer on and off via octoprint and the psu control addin. Wired up via a 3.3v relay.
2) 28 individually adressable leds individually controlable via octoprint and the Ws281x LED status plugin. (More on this later)
3) Titan aero clone, new bed springs, new belts, new pully bearings, new t8's, new antibacklash nuts.
4) pi cam. Not yet installed.
I think im about to pull out the last few original wires. Also @deuse this bed glass sheet flexi thing... where did you buy it.. I think I need a new one as i've managed to dig into it with something and there is a little gouge out of it

Last edited: