Bit more work done.
After thinking for a while about what there is actually left to do now that i've cut all the rot out of the shell I figured I was starting to get to a point where I needed the welding done before i could do much else, i considered doing the engine swap but that iteslf brought up a set of issues. Firstly i'd need to paint the engine bay and therefore would have to fork out for the spraying equipment earlier than intended as well as buy all the paint & materials, also the welding was due to be done around late July/early August so i'd have to have the engine in and running by then or have no way of getting the car out onto the trailer, that means relocating the battery, new radiator, hoses, loads of wiring, new downpipes made, spending money on the engine itself (new cams & injectors, checking timing tensioners, painting engine).
I just thought stuff it and went & spent £215 on a Clarke Pro 90 Mig Welder with no welding experience whatsoever!
I have since watched plenty of videos and had some practice on sheet metal where i can get nice smooth welds, but it's not so easy welding in awkward places.
I've since rebuilt the passenger side wing mounting rail out of Zintec.
New mounting rail is a perfect fit, i was rather pleased!
And i've welded a new passenger side floor corner in.
After thinking for a while about what there is actually left to do now that i've cut all the rot out of the shell I figured I was starting to get to a point where I needed the welding done before i could do much else, i considered doing the engine swap but that iteslf brought up a set of issues. Firstly i'd need to paint the engine bay and therefore would have to fork out for the spraying equipment earlier than intended as well as buy all the paint & materials, also the welding was due to be done around late July/early August so i'd have to have the engine in and running by then or have no way of getting the car out onto the trailer, that means relocating the battery, new radiator, hoses, loads of wiring, new downpipes made, spending money on the engine itself (new cams & injectors, checking timing tensioners, painting engine).
I just thought stuff it and went & spent £215 on a Clarke Pro 90 Mig Welder with no welding experience whatsoever!

I have since watched plenty of videos and had some practice on sheet metal where i can get nice smooth welds, but it's not so easy welding in awkward places.
I've since rebuilt the passenger side wing mounting rail out of Zintec.
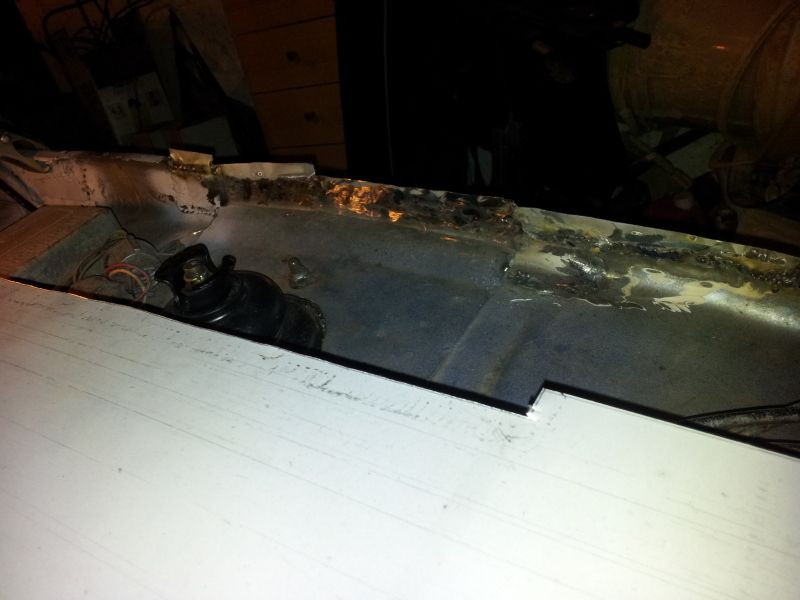
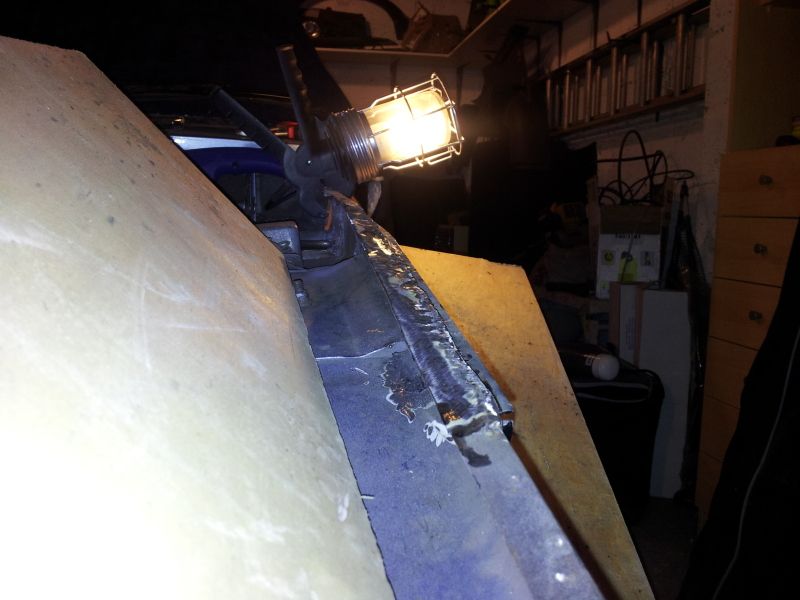
New mounting rail is a perfect fit, i was rather pleased!
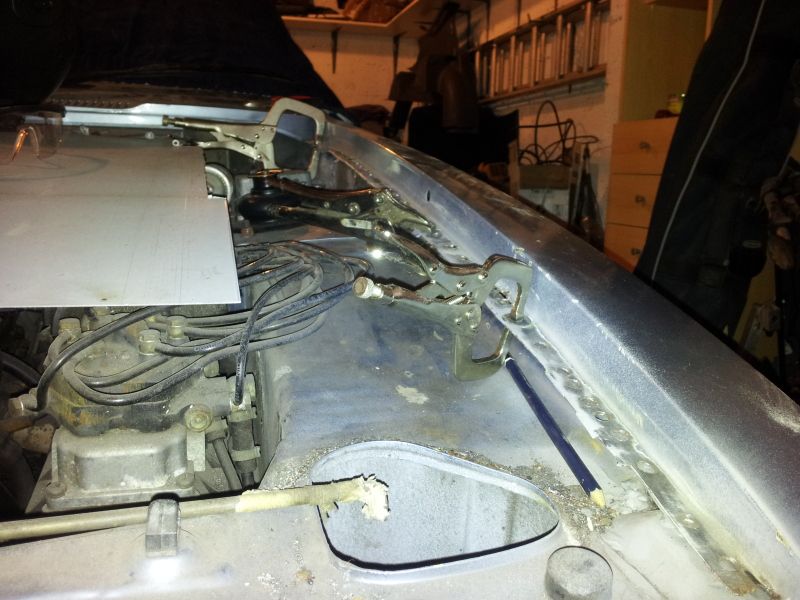
And i've welded a new passenger side floor corner in.
