Tried the new crimper today, it makes light work of crimping, but it is really heavy and cumbersome to hold, but it does beautiful crimps, crimped this one twice just to get a slightly longer crimp. With the other one you have to crimp multiple times, rotating the lug to get a nice crimp.
Started building up the second battery tray, cell's aren't arriving until late April, but there is plenty to do.
And also the main rack fuse and busbar.
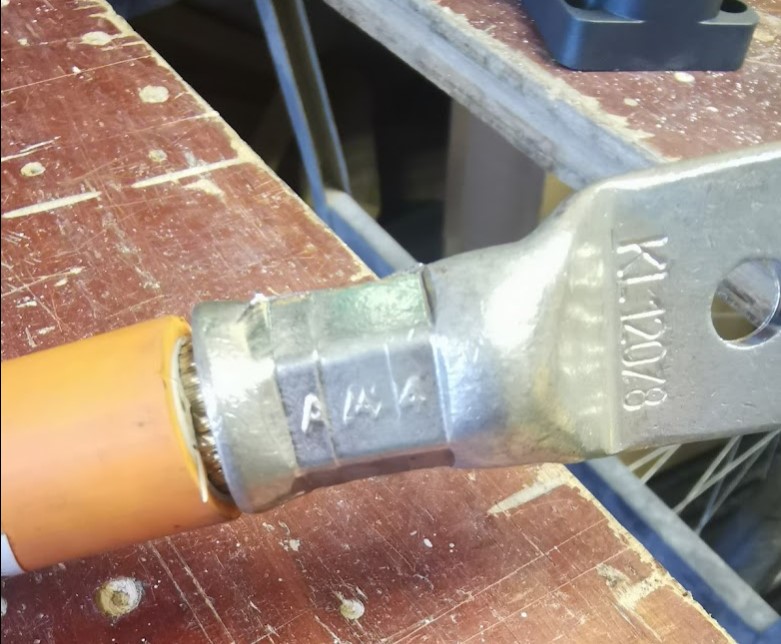
Started building up the second battery tray, cell's aren't arriving until late April, but there is plenty to do.
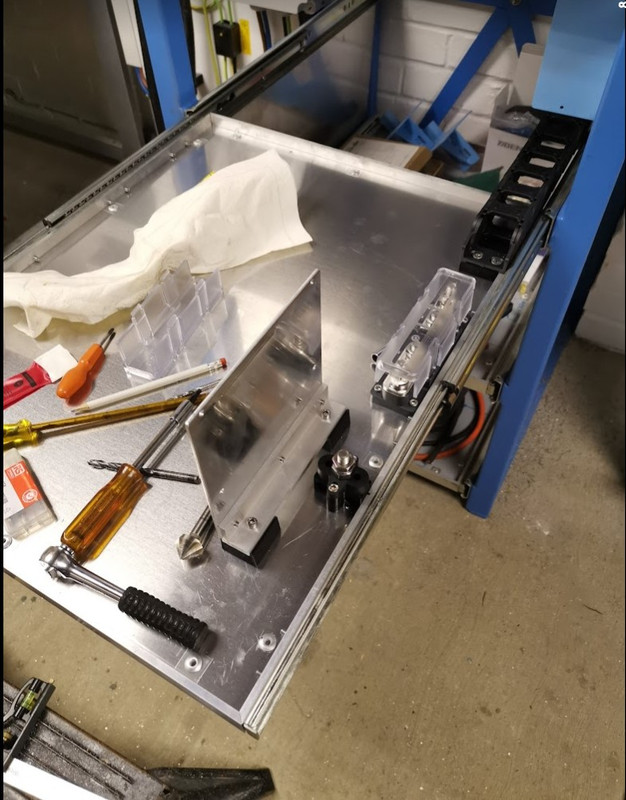
And also the main rack fuse and busbar.
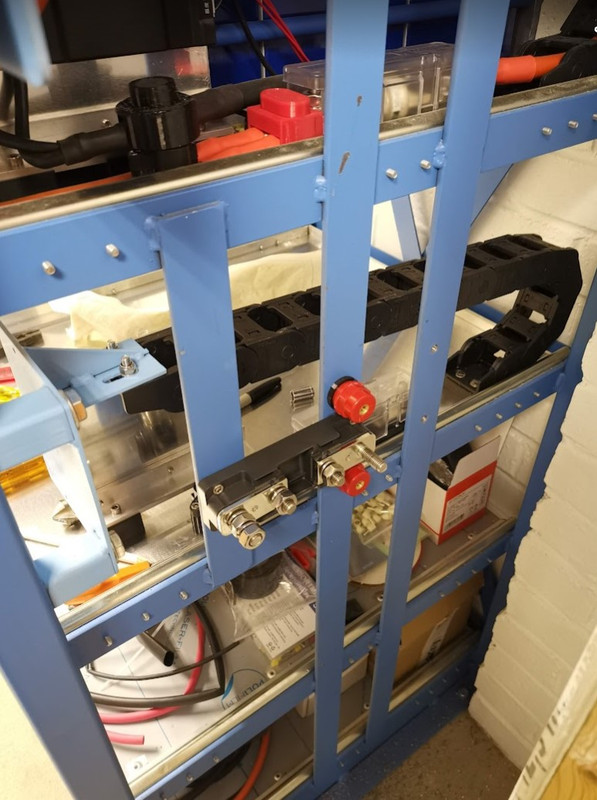