Right so thought I'd give some more details as I make the next actuators, especially since it's using an off the shelf screw and nut which makes it easier to replicate... The only thing that would be a very difficult without a lathe would be turning down the screw for the bearing block, but you can order screws with end machining if needed.
Here's a selection of most of the parts (mainly missing 4mm steel guide rods x3 and a 6mm to 6mm flexible coupling) :
32mm OD, 30mm ID CF tube
12mm OD, 10mm ID stainless steel tube
8mm trapezoidal lead screw (2mm lead, not the more common 8mm lead)
30mm m3 standoffs
6x19x6mm deep groove bearings and a couple of m6 washers to go between them.
3D printed parts (black parts are printed in a CF PETG composite, orange is Armadillo semi-rigid TPU, grey guide is just matt PLA)
Zhengke ZGA37RG 12v 1000rpm motor
First up turning down one end of the screws that it fits through the bearing block. A good tip here that I learned a while ago was to take it down to just a few tenths of a mm above where you need it to be, then use some 600 grit to massage it down to size until you can slip the bearing on... stops you overshooting end ending up with a loose fit.
Next I used a 10mm reamer to just make sure the ID of the steel tube was right to make fitting the nut easier.
That done, flipped it around and gave it a quick polish with some scotch pad followed by 2000 grit.
Polished section vs unpolished (that bit is getting cut off anyway!):
To finish the tube off, I just cut to length with an angle grinder and then popped it into the lathe again to ream the other end as above, as we'll be making a small part to attach to the rig.
Then it was simply a case of smacking the nut into the tube (it should be a tight fit, I used a hammer and some wood to avoid damaging the end of the tube or the nut) along with some thread lock/sleeve lock to help make sure it doesn't go anywhere.
Assemble the end bushing (when I eventually get a multmaterial printer it would be cool to be able to print this sort of thing as a single piece) and ream the ever-living poop out of it with a 12mm reamer until it's a snug but smooth slide fit on the 12mm rod:
Put the motor section together and we're most of the way towards building an actuator! More to come later.
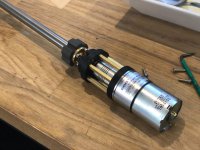
Here's a selection of most of the parts (mainly missing 4mm steel guide rods x3 and a 6mm to 6mm flexible coupling) :
32mm OD, 30mm ID CF tube
12mm OD, 10mm ID stainless steel tube
8mm trapezoidal lead screw (2mm lead, not the more common 8mm lead)
30mm m3 standoffs
6x19x6mm deep groove bearings and a couple of m6 washers to go between them.
3D printed parts (black parts are printed in a CF PETG composite, orange is Armadillo semi-rigid TPU, grey guide is just matt PLA)
Zhengke ZGA37RG 12v 1000rpm motor
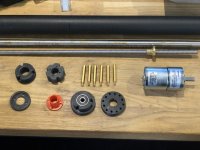
First up turning down one end of the screws that it fits through the bearing block. A good tip here that I learned a while ago was to take it down to just a few tenths of a mm above where you need it to be, then use some 600 grit to massage it down to size until you can slip the bearing on... stops you overshooting end ending up with a loose fit.
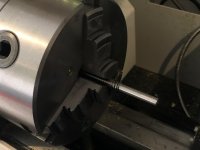
Next I used a 10mm reamer to just make sure the ID of the steel tube was right to make fitting the nut easier.
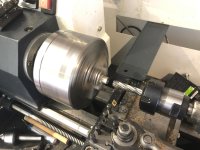
That done, flipped it around and gave it a quick polish with some scotch pad followed by 2000 grit.
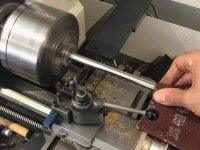
Polished section vs unpolished (that bit is getting cut off anyway!):
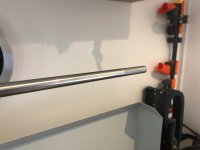
To finish the tube off, I just cut to length with an angle grinder and then popped it into the lathe again to ream the other end as above, as we'll be making a small part to attach to the rig.
Then it was simply a case of smacking the nut into the tube (it should be a tight fit, I used a hammer and some wood to avoid damaging the end of the tube or the nut) along with some thread lock/sleeve lock to help make sure it doesn't go anywhere.
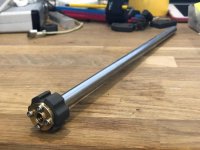
Assemble the end bushing (when I eventually get a multmaterial printer it would be cool to be able to print this sort of thing as a single piece) and ream the ever-living poop out of it with a 12mm reamer until it's a snug but smooth slide fit on the 12mm rod:
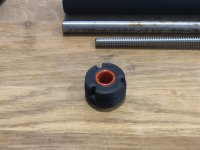
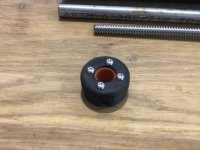
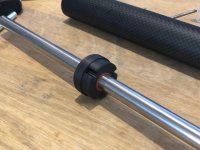
Put the motor section together and we're most of the way towards building an actuator! More to come later.
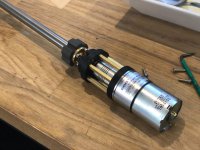
Last edited: