Bit of an update!
First things first The VRS Direct Force Pro came into stock, so I snapped one up. It was hand delivered by Matt who is the UK distributer since it turns out he lives just down the road from me! Have to say he's a top chap and we ended up having a chat for the better part of an hour
I machined up a mounting plate for it, the idea being it will be easy enough to hot swap this out for eg a Yoke if I want to add one in the future. It fits like a glove, almost as though it was made for it
Next job will be installing the control box under the rig and running the wires properly. I have to say I'm extremely impressed with the quality, they use good quality connectors and shielded lines to the motor. The control box is compact and very dense, a revelation compared to something like the open wheel control boxes if you are familiar.
In other news the motor mount I was waiting for arrived and I got it attached to the seat with a small printed part to adapt to the curvature.
Which then allowed me to mount my belt "backpack" (ignore the red tape holding the straps, I'll be making some clips to hold those)
And beyond that I've been prototyping my actuators, including how they'll mount to the rig. I've designed a system that uses cheap stainless steel strap and tightens with a little cam piece to grip the tube. I've mocked one up and it seems to work well.
I just took delivery yesterday of all the servo motors, but still waiting on many of the internal parts such as ball screws to arrive but I've made most of 1 actuator. Quite long 3d prints involved as I'm printing the parts fairly dense for strength. This is just a prototype and I'm not sure yet whether I will end up machining the main end pieces out of aluminium as it would be quicker and stronger, but takes more effort and material cost. I'm sort of interested in how well the 3d printer parts will hold up to the abuse so I'm tempted to go for all 3d printed for now.... certainly more accessible for others if they want to copy the design so would be good to know how well it works.
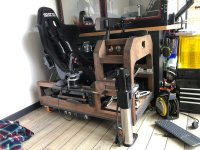
First things first The VRS Direct Force Pro came into stock, so I snapped one up. It was hand delivered by Matt who is the UK distributer since it turns out he lives just down the road from me! Have to say he's a top chap and we ended up having a chat for the better part of an hour

I machined up a mounting plate for it, the idea being it will be easy enough to hot swap this out for eg a Yoke if I want to add one in the future. It fits like a glove, almost as though it was made for it

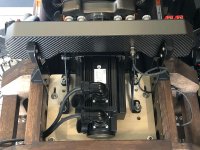
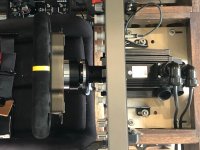
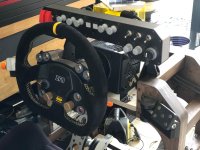
Next job will be installing the control box under the rig and running the wires properly. I have to say I'm extremely impressed with the quality, they use good quality connectors and shielded lines to the motor. The control box is compact and very dense, a revelation compared to something like the open wheel control boxes if you are familiar.
In other news the motor mount I was waiting for arrived and I got it attached to the seat with a small printed part to adapt to the curvature.
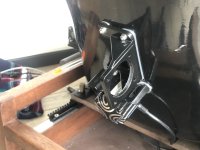
Which then allowed me to mount my belt "backpack" (ignore the red tape holding the straps, I'll be making some clips to hold those)
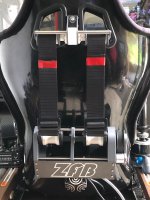
And beyond that I've been prototyping my actuators, including how they'll mount to the rig. I've designed a system that uses cheap stainless steel strap and tightens with a little cam piece to grip the tube. I've mocked one up and it seems to work well.
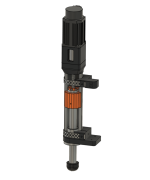
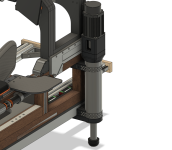
I just took delivery yesterday of all the servo motors, but still waiting on many of the internal parts such as ball screws to arrive but I've made most of 1 actuator. Quite long 3d prints involved as I'm printing the parts fairly dense for strength. This is just a prototype and I'm not sure yet whether I will end up machining the main end pieces out of aluminium as it would be quicker and stronger, but takes more effort and material cost. I'm sort of interested in how well the 3d printer parts will hold up to the abuse so I'm tempted to go for all 3d printed for now.... certainly more accessible for others if they want to copy the design so would be good to know how well it works.
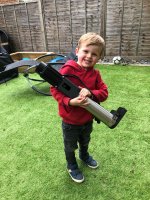
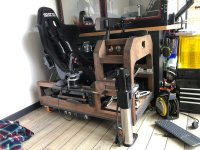