Thanks again gents!
to address more specifics:
I’m an airbus pilot normally, but I’m off for the winter thanks to the virus...
re the buttkickers no, the amp is arguably overkill but I picked it up much cheaper than the official single channel buttkicker amp, and it’s a 2 channel beasty with really useful USB connection to the PC for some handy settings.
I can massively recommend the buttkicker route, it adds so much immersion in VR that the sim feels broken now if they aren’t turned on.
Are you chaps referring to the pedals? I must admit I’ve considered the idea of making at least one limited run batch and seeing if anyone wants to buy, but obviously there’s a not-insignificant upfront investment in materials and time required and the market isn’t short of pedal options.
I also really need to nail down a clutch design, even though I don’t really use one at the moment (need to build a shifter!).
Speaking of the pedals though I’ve just oiled up the plywood pedal plate up and it’s looking much better - just need to decide what to do for a foot rest. I can’t decide if it should be grippy (eg grip tape) or slippy (eg aluminium plate).
I also got the new chunky shock damper for the brake.
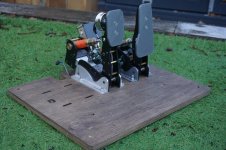
to address more specifics:
Apologies if you've covered it and I missed it, what do you do for a living?
I really want to add butt kickers at some point, is an amp that size a requirement?
I’m an airbus pilot normally, but I’m off for the winter thanks to the virus...
re the buttkickers no, the amp is arguably overkill but I picked it up much cheaper than the official single channel buttkicker amp, and it’s a 2 channel beasty with really useful USB connection to the PC for some handy settings.
I can massively recommend the buttkicker route, it adds so much immersion in VR that the sim feels broken now if they aren’t turned on.
As always mate, incredible work. You could make a serious killing out of these if you ever decided to manufacturer them. I'm sure the Sim boys would die for something like this even if you charged £££££.
If you didn't want to go to the effort of manufacturing it you could sell blueprints, stls and dxf files.
Are you chaps referring to the pedals? I must admit I’ve considered the idea of making at least one limited run batch and seeing if anyone wants to buy, but obviously there’s a not-insignificant upfront investment in materials and time required and the market isn’t short of pedal options.
I also really need to nail down a clutch design, even though I don’t really use one at the moment (need to build a shifter!).
Speaking of the pedals though I’ve just oiled up the plywood pedal plate up and it’s looking much better - just need to decide what to do for a foot rest. I can’t decide if it should be grippy (eg grip tape) or slippy (eg aluminium plate).
I also got the new chunky shock damper for the brake.
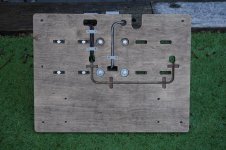
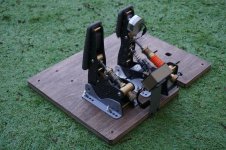
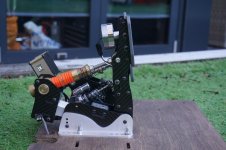
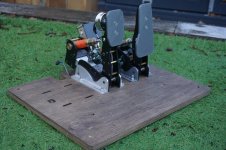
Last edited: