Right, I think we're done! (well mostly, but I'll get to that!)
Last tube run was a delight. Not a massively complex compound bend but something always seemed to trash each attempt. Got it done, in and pressure tested. Dual motherboard USB header to Aquaero and Farbwerk made up and sleeved. Sleeved a temp sensor and (kapton) taped it to the right angle fitting immediately behind the pump outlet. Should do the job. Well, that's what I thought but it turned out that I'd managed to pick the only one that one of the traces had fractured....so it did nothing and I had to make another. Not the end of the world - the fans just ran full speed due to lack of input (and I'd set the curve for 100% at 0°C for just that reason) - but irritating none the less.
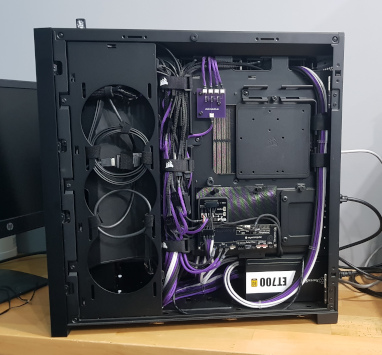
Inner door on - to hide all that I've made look tidy
Had some fun with the power plug for the Aquaero being just too high for the door to shut properly. Was massively overthinking how to fix it....until it dawned on me that it might just push slightly further into the socket! *facepalm*
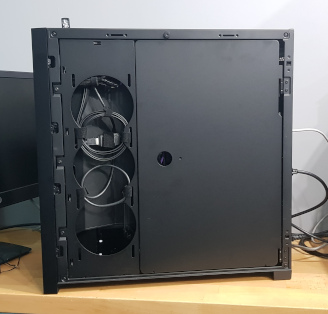
There's an outer panel that goes on after that which I've neglected to take a picture of for some reason...but there's a mini gamer-in-training occupying the rig now!
From the front showing the pump to GPU link and the GPU to CPU link in place.
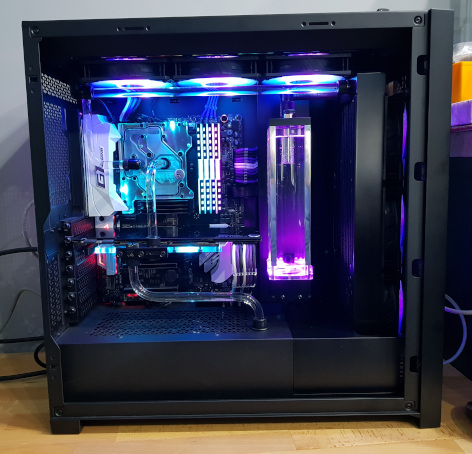
And with the outer door on.
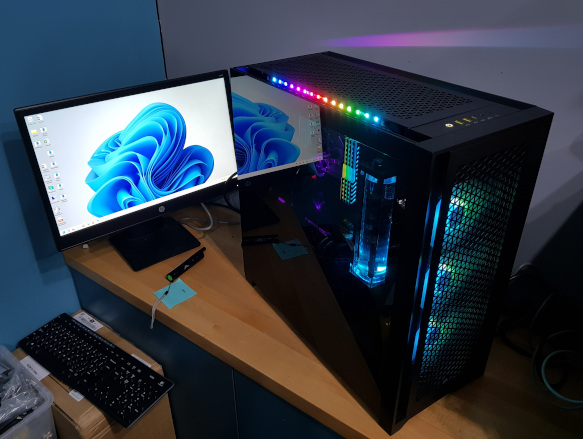
Ran some 3D Mark and it came out "Good" and above average scores. The CPU is a 6700K (that's Sky Lake, 4 core, 4GHz) but the turbo is turned up from 4.2GHz to 4.4GHz on all cores simultaneously. Also delidded and liquid metal applied - that's all from its previous occupation as my computer. GPU is a 980Ti with an identity crisis - the backplate claims it's a Titan X....but that's all I could get when I originally blocked it.
So what's left if it's not totally complete? Well, when it came to letting my son press the button to turn it on for the first time, it lit up and LIVED....and then the PSU went *CLACK* and everything died....and stayed dead
Took me some stripping down and some swearing to work out what the problem was. Turns out that if the sense wires are plugged into the PSU, it has kittens and dies. With it unplugged and some recovery time or full power cycle, it runs nicely. I think that I've simply got the order flipped but it's not listed anywhere and Silverstone don't seem to have any support (that I could find on their website) so I've posted up in the PSU forum to see if anyone can confirm the pinout rather than risk guessing and letting out the magic smoke!
That, would be the last bit and then it can go in its final place.....or at least it can once I can make it stop raining through the roof right above it 
Last tube run was a delight. Not a massively complex compound bend but something always seemed to trash each attempt. Got it done, in and pressure tested. Dual motherboard USB header to Aquaero and Farbwerk made up and sleeved. Sleeved a temp sensor and (kapton) taped it to the right angle fitting immediately behind the pump outlet. Should do the job. Well, that's what I thought but it turned out that I'd managed to pick the only one that one of the traces had fractured....so it did nothing and I had to make another. Not the end of the world - the fans just ran full speed due to lack of input (and I'd set the curve for 100% at 0°C for just that reason) - but irritating none the less.
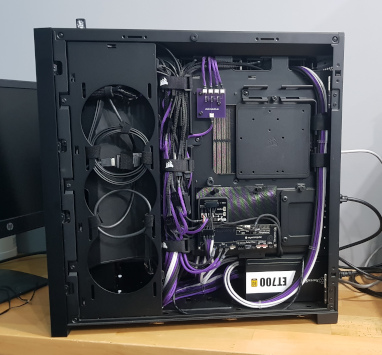
Inner door on - to hide all that I've made look tidy

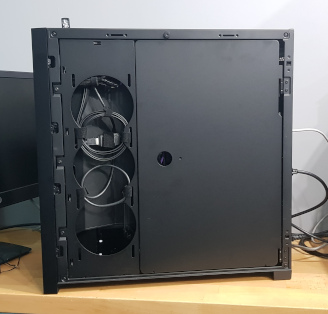
There's an outer panel that goes on after that which I've neglected to take a picture of for some reason...but there's a mini gamer-in-training occupying the rig now!
From the front showing the pump to GPU link and the GPU to CPU link in place.
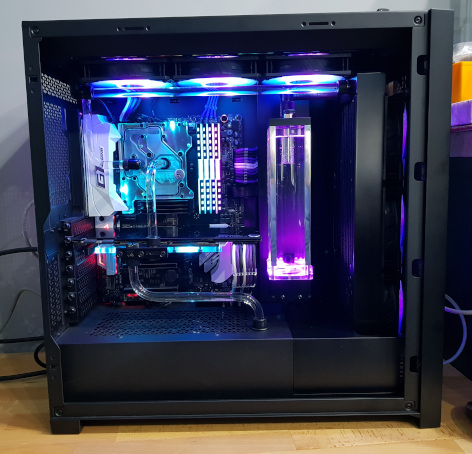
And with the outer door on.
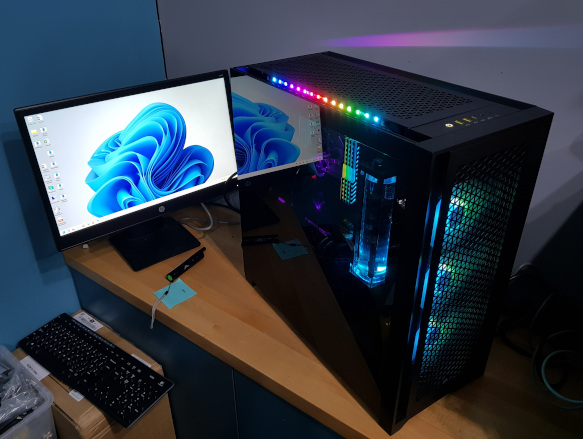
Ran some 3D Mark and it came out "Good" and above average scores. The CPU is a 6700K (that's Sky Lake, 4 core, 4GHz) but the turbo is turned up from 4.2GHz to 4.4GHz on all cores simultaneously. Also delidded and liquid metal applied - that's all from its previous occupation as my computer. GPU is a 980Ti with an identity crisis - the backplate claims it's a Titan X....but that's all I could get when I originally blocked it.
So what's left if it's not totally complete? Well, when it came to letting my son press the button to turn it on for the first time, it lit up and LIVED....and then the PSU went *CLACK* and everything died....and stayed dead


